Elio Motors Momentum v56
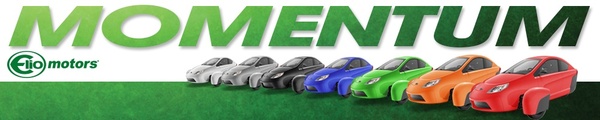
Behind the Scenes: Computer Aided Engineering Expertise
As part of the conception, development and launch of any new vehicle, including the Elio, automotive engineers perform a series of Computer Aided Engineering (CAE) evaluations to appraise safety performance, durability, aerodynamic performance, and general vehicle stiffness. Long before real “hardware” is available for testing, these computer simulations provide valuable data in predicting the vehicle’s capability of absorbing an impact and protecting the occupant, predicting the life of the vehicle structure subjected to long-term mileage accumulation, determining the aerodynamic drag of the vehicle to design for fuel economy, and obtaining the necessary structural performance for handling and noise, vibration and harshness considerations.
CAE has allowed the engineering team to make adjustments to the Elio prior to actual physical tests, which significantly helps to reduce both cost and time to market.
Safety: one of four core Elio Motors tenets
Before the Elio endures an actual, physical impact test, CAE provides the Elio Motors’ engineers the insight necessary to effectively design and tune the appropriate crush zones into the vehicle prior to being manufactured. Which is a valuable step given in a real-world situation, crush zones are what will create a deformation in the vehicle’s structure to control the dissipation of energy and better protect occupants.
“We’re following industry-standard practices as we strive to propel the Elio above and beyond in providing safety,” said Jeff Johnston, Vice President of Engineering for Elio Motors. “Whether front, back, or sides, the Elio has been developed by the engineering team using a combination of solid engineering principles and design creativity in order to provide the best protection possible for occupants.”
When it comes to safety engineering, Johnston explained that the Elio has longer nose and tail areas with plenty of real estate in which crush zones can be engineered to absorb energy. The sides of the vehicle require more attention regarding occupant protection. The Elio’s pillars come into play in anchoring side-impact protection. These are designed to stay stiff and not bend, buckle, or deform. The cross members in the underfloor and roof also are important in absorbing energy.
The other strategy in energy absorption is tying together the entire safety cage of the vehicle frame as a system. This includes the impact beams that are in the door and right side panel, which play a strong role and tie the entire side of the vehicle together with the vehicle’s pillars. If a vehicle experiences a severe side impact, the beams minimize intrusion and transfer energy to other parts of the vehicle, much like tendons in a person’s arm or leg might pull or stretch to transfer energy or weight in order to absorb a load. The goal is to distribute this energy load around the passengers toward the front and rear of the vehicle.
CAE impact simulation - front view
CAE impact simulation - bottom view
Restraint optimization ensures harmony between seat belts, air bags
The other key to occupant safety is restraints optimization. This is the process of ensuring the seatbelt and airbags work together in terms of belt payout (the amount of travel in the belt and occupant movement during an impact event), airbag deployment timing, and airbag venting to cushion the occupant during deployment.
The Elio also will embrace the LATCH (Lower Anchors and Tethers for Children) system for the passenger seat, which was developed to make it easier to correctly install child safety seats without using seat belts. LATCH can be found in infant, convertible, and forward-facing child safety seats made after Sept. 1, 2002.
As the Elio moves past its engineering phase into its E-Series build phase, know that safety, in terms of body and chassis design and occupant restraint systems, has been thoroughly engineered into the vehicle by Elio Motors in concert with key top tier safety systems suppliers well in advance of the rubber ever hitting the road.
Behind the Scenes: Computer Aided Engineering Expertise
As part of the conception, development and launch of any new vehicle, including the Elio, automotive engineers perform a series of Computer Aided Engineering (CAE) evaluations to appraise safety performance, durability, aerodynamic performance, and general vehicle stiffness. Long before real “hardware” is available for testing, these computer simulations provide valuable data in predicting the vehicle’s capability of absorbing an impact and protecting the occupant, predicting the life of the vehicle structure subjected to long-term mileage accumulation, determining the aerodynamic drag of the vehicle to design for fuel economy, and obtaining the necessary structural performance for handling and noise, vibration and harshness considerations.
CAE has allowed the engineering team to make adjustments to the Elio prior to actual physical tests, which significantly helps to reduce both cost and time to market.
Safety: one of four core Elio Motors tenets
Before the Elio endures an actual, physical impact test, CAE provides the Elio Motors’ engineers the insight necessary to effectively design and tune the appropriate crush zones into the vehicle prior to being manufactured. Which is a valuable step given in a real-world situation, crush zones are what will create a deformation in the vehicle’s structure to control the dissipation of energy and better protect occupants.
“We’re following industry-standard practices as we strive to propel the Elio above and beyond in providing safety,” said Jeff Johnston, Vice President of Engineering for Elio Motors. “Whether front, back, or sides, the Elio has been developed by the engineering team using a combination of solid engineering principles and design creativity in order to provide the best protection possible for occupants.”
When it comes to safety engineering, Johnston explained that the Elio has longer nose and tail areas with plenty of real estate in which crush zones can be engineered to absorb energy. The sides of the vehicle require more attention regarding occupant protection. The Elio’s pillars come into play in anchoring side-impact protection. These are designed to stay stiff and not bend, buckle, or deform. The cross members in the underfloor and roof also are important in absorbing energy.
The other strategy in energy absorption is tying together the entire safety cage of the vehicle frame as a system. This includes the impact beams that are in the door and right side panel, which play a strong role and tie the entire side of the vehicle together with the vehicle’s pillars. If a vehicle experiences a severe side impact, the beams minimize intrusion and transfer energy to other parts of the vehicle, much like tendons in a person’s arm or leg might pull or stretch to transfer energy or weight in order to absorb a load. The goal is to distribute this energy load around the passengers toward the front and rear of the vehicle.
Restraint optimization ensures harmony between seat belts, air bags
The other key to occupant safety is restraints optimization. This is the process of ensuring the seatbelt and airbags work together in terms of belt payout (the amount of travel in the belt and occupant movement during an impact event), airbag deployment timing, and airbag venting to cushion the occupant during deployment.
The Elio also will embrace the LATCH (Lower Anchors and Tethers for Children) system for the passenger seat, which was developed to make it easier to correctly install child safety seats without using seat belts. LATCH can be found in infant, convertible, and forward-facing child safety seats made after Sept. 1, 2002.
As the Elio moves past its engineering phase into its E-Series build phase, know that safety, in terms of body and chassis design and occupant restraint systems, has been thoroughly engineered into the vehicle by Elio Motors in concert with key top tier safety systems suppliers well in advance of the rubber ever hitting the road.